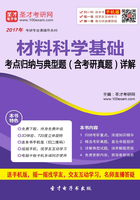
第4章 晶体的形变与断裂
4.1 考点归纳
一、弹性和黏弹性
1.弹性变形的本质
弹性变形是指外力去除后能够完全恢复的那部分变形,当无外力作用时,晶体内原子间的结合能和结合力可通过理论计算得出,它是原子间距离的函数,如图4-1所示。

图4-1 晶体内的原子间的结合能和结合力
(a)体系能量与原子间距的关系(b)原子间作用力和距离的关系
原子处于平衡位置时,其原子间距为r0,势能U处于最低位置,相互作用力为零。当原子受力偏离其平衡位置时,原子间距增大时将产生引力;原子间距减小时将产生斥力,外力去除后,原子都会恢复其原来的平衡位置,所产生的变形便完全消失,这就是弹性变形。
2.弹性变形的特征和弹性模量
弹性变形的主要特征是:
(1)理想的弹性变形是可逆变形,加载时变形,卸载时变形消失并恢复原状;
(2)金属、陶瓷和部分高分子材料不论是加载或卸载时,只要在弹性变形范围内,其应力与应变之间都保持单值线性函数关系,即服从胡克定律:
①在正应力下:σ=Eε,
②在切应力下:τ=Gγ,
弹性模量与切变弹性模量之间的关系为:

式中,υ为材料泊松比,表示侧向收缩能力,在拉伸试验时系指材料横向收缩率与纵向伸长率的比值。
弹性模量代表着使原子离开平衡位置的难易程度,反映原子间结合力,是表征晶体中原子间结合力强弱的物理量。
(3)弹性的不完整性
①包申格效应
材料经预先加载产生少量塑性变形,而后同向加载则σe升高,反向加载则σe下降。
②弹性后效
在弹性极限范围内,应变滞后于外加应力,并和时间有关的现象称为弹性后效或滞弹性。
③弹性滞后
由于应变落后于应力,在σ-ε曲线上使加载线与卸载线不重合而形成一封闭回线,称之为弹性滞后,如图4-2所示。

图4-2 弹性滞后(环)与循环韧性
(a)单向加载弹性滞后(环)(b)交变加载(加载速度慢)弹性滞后(c)交变加载(加载速度快)弹性滞后(d)交变加载塑性滞后(环)
④黏弹性
黏弹性变形既与时间有关,又具有可回复的弹性变形性质,即具有弹性和黏性变形两方面的特征。特点是应变落后于应力,当加上周期应力时,应力一应变曲线就成一回线,所包含的面积即为应力循环一周所损耗的能量,即内耗。
二、塑性变形的概念
当外加应力超过一定值(即屈服极限)时,应力和应变就不再呈线性关系,卸载后变形也不能完全消失,而会留下一定的残余变形或永久变形。
三、滑移系统和Schmid定律
1.晶体的滑移系统
晶体的滑移系统首先取决于晶体结构,但也与温度、合金元素等有关。常温、常压下各种晶体结构的滑移系统如表4-1所示。
表4-1 各种晶体的滑移系统和临界分切应力

2.Schmid定律
(1)剪应力
由于滑移是晶体沿滑移面和滑移方向的剪切过程,决定晶体能否开始滑移的应力一定是作用在滑移面上沿着滑移方面的剪应力,或称为分切应力。
(2)Schmid定律表达式
作用在滑移面上沿着滑移方向的分切应力为:

式中,为拉伸应力;
,称为取向因子或Schmid因子。
(3)Schmid定律的应用
当晶体具有等价的滑移系统时,利用Schmid定律便可确定在给定方向加载(拉伸或压缩)时滑移首先沿哪个或哪些系统进行,是单滑移、双滑移还是多滑移。
3.滑移时参考方向和参考面的变化
(1)参考方向的变化

图4-3 滑移过程中参考方向的变化
(a)滑移前;(b)滑移后;(c)相对位移
(2)参考面的变化
①试样轴向的变化

②试样端面的变化

4.滑移过程中晶体的转动
(1)晶体转动的原因
在自由滑移时,试样的轴(参考方向)和端面(参考面)在空间的方位一般都要改变。可是在通常的力学试验中,由于夹头对试样的约束,其方位是不能随意改变的;
对多晶体来说,由于晶界、缺陷、杂质等的约束作用,各晶粒在滑移过程中也伴随着转动。
(2)晶体转动的规律
单晶体在拉伸时滑移方向力图转向(或趋近)拉伸轴;压缩时则滑移面力图转向(或趋近)压缩面(即端面)。
(3)晶体转动的后果
①试样长度的变化
单晶试棒在拉伸时会伸长,伸长量取决于晶体的位向和切变量γ:

利用体积不变的关系,得到:

②试样的位向变化和双滑移
单晶试棒在拉伸或压缩时位向会不断改变,晶体位向的变化可能引起滑移方式的变化,即由单滑移变成双滑移。
③几何软化
单晶体在拉伸试验初期,拉应力F会随着变形量的增加而减小,这种现象是由于晶体位向变化引起的,故称为几何软化。
5.滑移过程的次生现象
(1)晶面弯曲
由于局部区域的微观缺陷、杂质等的阻碍作用,滑移面可能发生弯曲,这种弯曲的晶面可近似地看成由一系列位向差很小的平面组成。
(2)形变带
由于局部区域存在杂质和各种缺陷,这些区域的转动就受到阻碍,其转角小于远离杂质和缺陷的区域,产生位向差,因而在显微镜下存在反差(衬度)。
(3)弯折带
基面近乎平行于压力方向的锌(或镉)单晶在压缩试验时会发生弯折现象。
6.单晶体的硬化曲线
(1)硬化概念
(物理)硬化是指在滑移过程中由于晶体内部结构(主要是位错的密度、分布和性质等)的变化,继续维持滑移所需的切应力随切变量τ的增大而不断增加的现象。
(2)硬化曲线
应变硬化曲线是指描述单晶体应变硬化行为的曲线,通常也就是晶体在拉伸时的切应力-切变曲线。以面心立方为例,应变硬化曲线如图4-4所示。

图4-4 FCC晶体典型的应变硬化曲线
(3)硬化的参量
①硬化量τh
硬化量等于流变应力τ与临界分切应力τc的差值,即τh=τ-τc。
②硬化率(或硬化系数)
根据硬化率可以将硬化曲线分为三个阶段:
a.第I阶段:易滑移阶段,dτ/dγ非常小;
b.第II阶段:线性硬化阶段,dτ/dγ为一恒定的最大值;
c.第Ⅲ阶段:抛物线硬化阶段,dτ/dγ随着γ增加而减小。
四、孪生系统和原子的运动
1.晶体的孪生系统
晶体的孪生系统主要取决于晶体结构。晶体的孪生系统如下:
(1)FCC晶体的孪生系统是{111}<112>;
(2)BCC晶体的孪生系统是{112}<111>;
(3)HCP晶体的孪生系统是。
2.孪生时原子的运动和特点
(1)原子运动的规则
①原子的最终位置要与基体中的原子构成映像关系,镜面就是孪生面;
②最小位移原则:根据最小功原理,原子移动的距离应最小。
(2)孪生的特点
①孪生不改变晶体结构;
②孪晶与基体的位向不同,二者的位向关系是确定的;
③孪生时,平行于孪生面的同一层原子的位移均相同,位移量正比于该层到孪生面的距离;
④孪生时堆垛次序的变化
a.在孪生面右下方(基体部分),堆垛次序是ABCABC;
b.在孪生面左上方(孪晶部分),堆垛次序为CBACBA;
c.如果将字母顺序ABCABC…视为正常顺序,那么AC、CB、BA等顺序均属层错。
(3)孪晶界面能
位于均匀介质内部的原子受周围原子作用的合力为零,处于能量最低的状态。
3.孪生要素和长度变化规律
(1)孪生引起的形状变化
由于平行于孪生面的各层都沿孪生方向位移,且位移量正比于该层到孪生面的距离,所以孪生是一种均匀变形。
(2)孪生四要素
K1, η1, K2, η2称为孪生四要素。对一定的晶体结构,孪生四要素都是确定的。
(3)孪生时长度变化规律
①凡是位于K1和K2面相交成锐角区域的晶向,孪生后必缩短;
②凡是位于K1和K2面相交成钝角区域的晶向,孪生后必伸长。
4.孪生时试样的最大伸长和最大缩短量
(1)最大伸长为:

(2)最大缩短为:

5.滑移和孪生的比较
表4-2 滑移和孪生的比较

五、多晶体范性形变的一般特点
1.晶粒边界
(1)概念
多晶材料是由许多取向不同的小单晶体即晶粒组成的,晶粒边界(简称晶界)是指晶粒和晶粒之间的过渡区域。
(2)晶界在多晶体范性形变中的作用
①协调作用
多晶体是一个整体,各晶粒的变形不能是任意的,而必须相互协调,否则在晶界处就会裂开。
②障碍作用
在低温或室温下变形时,滑移主要在晶粒内进行,它不可能穿过晶界而在相邻晶粒内进行。
③促进作用
在高温下变形时,除了晶粒内滑移外,相邻两个晶粒还会沿着晶界发生相对滑动。
④起裂作用
一方面,由于晶界阻碍滑移,此处往往应力集中;另一方面,由于杂质和脆性,第二相往往优先分布于晶界,使晶界变脆。因此,在变形过程中裂纹往往起源于晶界。
2.多晶体范性形变的微观特点
(1)多方式
多晶体的范性形变方式除了滑移和孪生外,还有晶界滑动和迁移,以及点缺陷的定向扩散。
(2)多滑移
与单晶体不同,多晶体变形时开动的滑移系统不仅仅取决于外加应力,而且取决于协调变形的要求。
(3)不均匀
与单晶体相比,多晶体的范性形变更加不均匀。
(4)其他特点
①产生内应力;
②出现加工硬化;
③形成纤维组织(杂质和第二相择优分布);
④择优取向(织构)。
3.晶粒度及其对性能的影响
(1)晶粒度概念
晶粒度是指晶粒的大小。
(2)晶粒度对性能的影响
①晶粒越细,阻碍滑移的晶界便越多(或晶界面积越大),屈服极限也就越高。大多数金属的屈服极限σy与晶粒度d有以下关系:

式中,σ1和K都是常数。这个公式称为Hall-Petch公式。
②金属的硬度与晶粒度也有一定的关系:

式中,HV或HB分别是维氏或布氏硬度。
③晶粒度对晶体的形变硬化行为也有很大的影响。
六、冷加工金属的储能和内应力
1.冷加工影响
(1)冷加工会引起点阵畸变或晶格扭曲;
(2)冷加工既可引起宏观内应力,也可引起微观内应力。
2.内应力的危害
(1)内应力可能叠加在工作应力上,使零件在使用时过早破坏或产生过量的塑性变形;
(2)内应力可能叠加在加工应力上,使材料在加工时开裂;
(3)储能和内应力可以加速退火过程;
(4)储能和内应力使金属在化学上更不稳定,因而容易被腐蚀。
七、应变硬化
1.应变硬化现象
(1)应变硬化概念
金属对塑性变形的抗力是随变形量的增加而增加的,应变硬化是指这种流变应力随应变的增加而增加的现象。
(2)单晶体和多晶体硬化曲线的差别
①对单晶体,流变应力是指作用在滑移面上沿着滑移方向的剪应力(分切应力)τ,而应变则是指剪应变(或切变)γ;
②对多晶体,应变是指在主流动方向(主要变形方向)的变形量,流变应力则是指引起该应变的应力。
2.实际晶体的硬化行为
FCC晶体的硬化特点如下:
(1)屈服极限比较低,往往低于其他晶体;
(2)硬化速率比较高,往往高于其他晶体;
(3)延伸率高,即塑性好。
3.影响应变硬化的因素
(1)变形温度
一般,温度越高,屈服极限越低,硬化速率也越小,具体的影响还与金属种类有关。
(2)变形速度
原子热运动(或称热激活)会促进塑性变形,而热运动不但与温度有关,而且与变形速度有关。因此,增加变形速度就相当于降低温度。
(3)晶粒度
晶粒越细,屈服极限及硬度越高。
(4)合金元素
从力学性能上讲,加合金元素大都是为了强化金属,即提高屈服极限和硬化速率,或延长硬化阶段。
4.应变硬化在生产实际中的意义
(1)不利方面
①由于金属在加工过程中塑性变形抗力不断增加,使金属的冷加工需要消耗更多的功率;
②由于应变硬化使金属变脆,因而在冷加工过程中需要进行多次中间退火使金属软化,能够继续加工而不致裂开;
③有的金属尽管某些使用性能很好,但由于解决不了加工问题,其应用受到很大限制。
(2)有利方面
①有些加工方法要求金属必须有一定的加工硬化;
②可以通过冷加工控制产品的最后性能;
③有些零部件在工作条件表面会不断硬化,以达到表面耐冲击、耐磨损的要求。
八、多晶材料的择优取向(织构)
1.概述
择优取向(简称织构)是指金属在冷加工以后各晶粒的位向分布关系。
2.织构的分类
(1)按织构的形成原因分类
如铸造织构、电镀织构、退火织构(或称再结晶织构)、加工织构等。
(2)按零件的外形分类
可将织构分为丝织构和板织构。
(3)按照共同晶向(或晶面)的个数分类
可将织构分为单织构和双织构。
3.织构的描述和测定方法
(1)织构的描述方法
①用晶向指数表示;
②用正极图表示;
③用反极图表示。
(2)织构的测定方法
①应用最广泛的方法是X光衍射方法;
②电子衍射方法也得到一定的应用;
③有时采用光学方法测织构;
④通过测定不同方向的磁学性质来测定织构。
九、晶体的断裂
1.晶体的断裂分类
表4-3 用不同方法对晶体的断裂进行分类

2.脆性断裂的微观理论——Griffith裂缝理论
(1)概念
固体的理论断裂强度就是没有微裂缝的理想固体的断裂强度σ0。
(2)固体理论断裂强度的计算公式

(3)Griffith裂缝
固体中本来就存在着某种微裂缝,这种裂缝就称为Griffith裂缝。

图4-5 Griffith裂缝
(4)理论强度表达式

表示Griffith裂缝扩展所需的应力,也就是晶体的实际断裂强度。
3.金属脆性断裂的特点
(1)金属在断裂前往往或多或少都有一定的微观塑性变形;
(2)金属发生脆性穿晶断裂时往往沿着特定的晶面裂开(拉断),这个晶面就称为解理面;
(3)将金属晶体沿解理面(沿法线方向)拉开所需的正应力是一定的,此应力称为该金属的临界(解理)正应力;
(4)金属脆性断裂的断口往往平整光亮,并与拉应力垂直;
(5)金属中一般不存在足以引起断裂的预裂缝;
(6)金属中裂缝的扩展过程十分复杂,可能导致各种各样的微观(断口)形貌。
4.影响金属的韧性、脆性和断裂的因素
(1)温度
温度越高,韧性越好;温度越低,则越脆。但影响的程度则与金属结构密切相关。
(2)应力状态
由于裂缝是在拉应力下扩展,故应力状态越硬,越易发生脆性断裂。
(3)加载速率(应变速率)
加载速率(或应变速率)对金属的塑性变形和断裂行为也有一定的影响,但影响远不如温度和应力状态等因素那样大,而且仅限于体心立方和密排六方金属。
(4)交变应力
如果材料受到大小和方向都随时间而周期性变化的交变应力作用,那么即使最大应力远低于屈服极限,材料也可能在一定的时间(或一定的应力交变次数)后发生断裂。
(5)环境和介质
①腐蚀脆化
a.影响表面能(或界面能),使形成裂缝所需的能量减小;
b.由于形成腐蚀坑或腐蚀产物而引起应力集中;
c.使金属零件的承载面积减少,平均应力增加,但一般情形下面积减少很有限,影响不大;
d.腐蚀介质沿高能缺陷区(位错、晶界、相界等处)渗透到金属内部,发生选择性腐蚀,大大削弱了晶体的结合力;
e.气体介质向金属内部扩散,引起金属脆化。
②辐照脆化
a.强度指标(屈服强度、强度极限、硬度、弹性模量等)增加,韧性指标(拉伸延伸率、断面收缩率、冲击韧性等)减小;
b.屈服强度的增加远超过强度极限(断裂强度)的增加;
c.屈服强度更急剧地随温度的减低而增加;
d.韧性-脆性转变温度升高;
e.拉伸时明显屈服点现象更明显。
(6)加工方式
不同的加工方式会产生不同的织构,从而在某些方向上出现脆性。
(7)晶体结构
一般来说,晶体的对称度越低或结构越复杂,金属就越脆。
(8)成分和组织
杂质,特别是氢、氧、氮、碳等间隙式杂质元素,会显著降低金属的塑性。
(9)晶粒度
与通常的合金元素的影响不同,细化晶粒不仅提高金属的强度,同时还提高其韧性。
十、金属的热变形、蠕变与超塑性.
1.金属热变形过程以及对组织与性能的影响
(1)金属热变形的定义
金属在再结晶温度以上的加工变形叫做热变形。
(2)金属的热变形过程
①它像冷加工那样发生晶粒的伸长与加工硬化;
②发生了回复和再结晶过程,又新形成了等轴晶粒与消除了加工硬化。
(3)动态回复和再结晶
回复和再结晶过程可以与变形同时产生的过程称为动态回复和再结晶。
2.金属的蠕变
(1)蠕变现象的产生
金属在室温下或者温度在低于0.3Tm时的变形,主要是通过滑移和孪晶两种方式进行的,而在温度高于0.3Tm。会发生位错的攀移,从而产生蠕变现象。
(2)蠕变的意义
蠕变是指材料在高温下的变形不仅与应力有关,而且与应力作用的时间有关。
(3)蠕变过程
①由蠕变速率逐渐减慢的第一阶段到稳态(恒速)蠕变的第二阶段;
②在蠕变过程后期,蠕变速率加快直至断裂是为蠕变第三阶段;
③随着温度与应力的增高,蠕变第二阶段渐短,金属的蠕变很快由第一阶段过渡到第三阶段,使高温下服役的零件寿命大大减少。

图4-6 典型的蠕变曲线

图4-7 蠕变速率和温度的关系
3.金属的超塑性
金属能显示超塑性的原因是:在一定温度下,流变应力和应变速率ε满足关系,
式中,m称为应变速率敏感系数。
十一、陶瓷晶体的变形
1.陶瓷难以变形的原因
无论是共价晶体陶瓷还是离子晶体型陶瓷,都是难以变形的,这是由它们结合键的本性决定的。
2.陶瓷晶体的强度
(1)陶瓷晶体的屈服强度一般在E/30,其理论屈服强度虽然很高,但实际的抗拉强度或断裂强度却很低;
(2)陶瓷的实际抗拉强度远低于理论的屈服强度,陶瓷的压缩强度总是高于抗拉强度;
(3)当裂纹长度为c,裂纹尖端的曲率半径为ρ,在名义应力σ的作用下,裂尖的最大应力:

十二、高分子材料(聚合物)的变形
1.热塑性塑料的变形
(1)对玻璃,在Tg以下只发生弹性变形,在Tg以上就产生粘滞性流动;
(2)对于热塑性塑料,其变形情况与玻璃相似;
(3)另一种极端情况,如得到结晶程度近于100%的塑料,那么其变形特性与金属相似。
2.热固性塑料的变形
热固性塑料是刚硬的三维网络结构,分子不易运动,在拉伸试验时表现出脆性金属一样的变形特性。