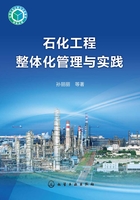
2.2 总流程规划集约化
2.2.1 总流程规划集约化目标和方法
基于集约化方法思路,总流程规划集约化是在全面识别项目内部资源要素和外部影响因素,以及详细分析资源特征和因素影响的基础上,通过信息化平台实施资源的全过程管理和统一优化配置,从而实现资源的高效利用和价值增值的过程方法。总流程规划集约化方法如图2-4所示。

图2-4 总流程规划集约化方法
总流程规划的内部资源要素主要包括原料、技术等,外部影响因素主要有产业政策、市场需求等。对于内部资源要素,主要分析项目原料的价值特征和工艺技术的功能特征;对于外部的影响因素,主要分析产业政策对项目的产品质量、安全生产及环保治理等方面的指标要求,以及市场需求对项目产品类型和产品结构的影响。在总流程规划集约化实施过程中,以项目的“高效益、低成本、低能耗、安全化、绿色化”为主要目标,利用PIMS等数字化工具开展项目资源的集中管理、统一配置、多目标、多方案的协调比选优化,保证项目的整体竞争力。
总流程规划集约化的内容主要包括以下方面[2]:
①根据石化产品的市场需求及所选原料性质确定建设规模。
②工艺技术方案的选择(了解和分析项目拟选用工艺技术的发展与应用状况)。
③装置的设置与联合方案。
④确定物料平衡,包括原料(含原料配置、辅助材料和燃料)与产品方案(含目标产品的组合、质量、数量要求)。
⑤全厂物流安排(上下游装置及储存设施是否稳定、是否做到合理衔接)。
⑥氢、硫、氮、蒸汽、燃料等关键组分/物料的平衡情况。
⑦确定投入物,如原材料、辅助材料、燃料、公用工程等的资源条件(规格、成分、质量、配置与供应状况等)。
⑧提高产品收率,降低加工能耗,提高经济效益。
⑨进行多方案比选,确定比选的主要内容,包括是否满足建设规模的要求,是否满足产品方案的要求,是否适应原料(原材料、辅助材料、燃料、公用工程等资源条件)的加工要求,是否达到安全、环保、操作的稳定与连续性、投资、效益的目标。
2.2.2 总流程规划集约化的过程实施
基于项目资源识别和特征分析,通过构建资源群组管理法,对加工方案进行集约化的规划配置,以满足建设需要。所谓资源群组管理法,就是以“群组”形式对同类石化工程项目原料资源进行集中转化,对中间资源进行二次集中利用,对产品资源进行集中管理,同时以“群组”形式对核心工艺装置、环保设施等进行技术集成和装置联合,实现物料和能量的节约使用。资源群组管理法示意图如图2-5所示。

图2-5 资源群组管理法
2.2.2.1 以资源群组管理方法实施物料资源集约化利用
(1)对原料资源实施集约化群组分类管理
以“结构”为特征对原料资源进行群组分类利用,以“价值”为特征对产品资源进行资源集中。
以炼厂方案规划为例,原油资源根据“分子结构”大小,大体划分为:重油-渣油、蜡油、柴油、石脑油、轻烃和气体六个群组,如图2-6所示。根据工艺要求或产品需求,上述群组可进一步依据“分子结构”特征进行资源的二次分类细化。以石脑油群组为例,可进一步划分为轻、重石脑油群组,轻石脑油群组依据正异构特征再次划分为正构和异构,正构石脑油群组依据“分子碳数”可进一步划分为碳五群组和碳六群组等。

图2-6 基于原料结构特征的群组分类管理
通过对原料进行由简到繁的“分子结构”特征组分类,群组资源的特点和价值经过层层分解,逐渐显现,将结构特征相同或相似的资源组群集中处理,装置规模扩大、数量减少,满足加工深度要求的同时,最大化减少占地,降低投资和后续生产运营成本,提高整体效益。
如对于炼厂副产的大量轻烃和气体资源,常规加工方案只对产量大且集中的催化裂化液化气等少量资源进行回收利用,其他轻烃和气体资源由于产量低、分布零散,通常作为低价值燃料外卖或自用,没有发挥高附加值。依据资源群组管理方法,将所有加氢装置副产低分气进行群组集中脱硫和变压吸附(PSA)处理,回收氢气量约占总耗氢量的10%,能够大幅度降低成本,为企业的降本增效做出贡献。另外通过对全厂所有装置副产饱和干气、不饱和干气中的碳二资源进行群组集中,可回收大量轻质化乙烯原料,降低乙烯装置生产成本。
以产品“价值”为特征的资源群组管理方面,最典型的是炼厂生产的车用汽油。通过调和多种不同“结构”和不同“价值”的单一组分,如催化汽油、异构化油、重整汽油等,使低价值的组分形成高价值的汽油产品,满足市场需要,符合国家标准规范要求,在此过程中汽油产品价值已远远超过了等量催化汽油、抽余油等单一资源的价值。
(2)对中间产品实施资源群组利用
在识别原料资源特征和群组分类的基础上,以“分子炼油”理念为指导,利用群组资源的分子结构优势实现资源利用价值的最大化,做到“物尽其用”。
在炼厂中,催化柴油富含60%~80%多环芳烃(质量分数),十六烷值为15~30,是一种非常劣质的柴油资源。对于催化柴油的利用,一般采用常规的加氢改质技术生产车用柴油,由于该技术氢耗高,反应条件苛刻,催化柴油中的芳烃组分未得到合理利用,尤其是在当前柴油严重过剩的市场形势下,这种高成本的利用方式未获得资源价值的提升。在资源群组法思路下,催化柴油的转化利用可以从其富含多环芳烃,尤其是双环芳烃结构的特征出发,引导双环芳烃分子利用自身的结构优势向高价值的目标产品转化。例如催化柴油加氢转化(RLG)就是基于该方法的一种催化柴油有效利用技术,它通过控制多环芳烃、双环芳烃部分加氢饱和及裂化路径,将催化柴油中的大分子芳烃转化为高价值的苯、甲苯、二甲苯等芳烃(BTX)资源和高辛烷值的汽油调和组分,实现了产品结构优化和经济效益提升。
对于直馏、加氢精制、加氢焦化、加氢裂化等石脑油资源,均可依据资源的结构特征进行群组分类和利用。如直馏轻石脑油、加氢精制石脑油和加氢焦化石脑油群组由于链烷烃含量高,适宜作为乙烯裂解原料;加氢裂化轻石脑油群组由于富含异构烷烃,辛烷值高,适宜作为汽油产品的调和组分;而直馏重石脑油和加氢裂化重石脑油群组由于芳潜值较高,适宜作为催化重整原料。
在乙烯装置中,为实现烯烃收率的最大化,一般根据乙烯原料的分子结构特征和裂解规律进行群组分类利用,如将轻烃群组、石脑油群组、柴油和加氢尾油群组资源分别送至不同操作条件的裂解炉进行高效转化;而将富乙烯气群组和裂解气体产物直接送至深冷分离单元进行烯烃高效回收;未反应的乙烷和丙烷资源继续返回裂解炉裂解成乙烯、丙烯,使每一份有价值的资源都得到最充分的利用。从乙烯生产流程可以看出,乙烯的生产过程就是利用群组资源的结构特征进行分子的逐级裂解,实现烃类大分子一步步转化为小分子乙烯、丙烯等过程。对于化工下游产业链而言,烯烃的利用过程更是基于分子水平的聚合和分解实现高品质、高端化工产品的生产。
(3)对外在因素影响下的产品资源群组利用
对于石化工程项目而言,外在影响因素主要有法律法规、产业政策、市场需求等,其中法律法规和产业政策影响着项目的品种选择、产品质量以及能耗、安全、环保等要求,市场需求影响着项目的产品结构、装置规模、产品产量等指标。
以产业政策和市场需求为导向,对资源进行质量评估和市场价值的评估,建立以产品质量和市场价值为特征的产品群组和非产品群组,对非产品群组资源进行引导式转化,并尽可能减少低市场价值产品的输出。
为减少机动车尾气排放污染,改善环境空气质量,促进绿色发展,我国成品油质量升级持续加快。2018年底全国的车用汽柴油质量均需满足国Ⅵ标准,从国Ⅴ到国Ⅵ,烯烃和芳烃含量限制更严格,造成降烯烃和提高辛烷值的双重压力[3]。
在市场需求方面,汽油市场基本趋于饱和,柴油市场已严重过剩,柴/汽需求结构不平衡;相对于油品消费势头的减缓,化工产品的需求明显增速。因此,为保证项目的高效益和竞争力,在总流程规划过程中需以“产业政策”和“市场需求”为导向,实现资源的群组转化。
炼厂柴油资源种类众多,性质千差万别,针对直馏柴油和二次转化的催化柴油、焦化柴油等资源,可依据市场需求对这类资源进行多途径利用(如图2-7所示)。在以“芳烃”为核心产品的企业中,低品质的催化柴油富含芳烃结构,可采用催化裂化劣质柴油生产高辛烷值汽油或轻质芳烃(LTAG)、RLG等工艺路线来增产高品质汽油和芳烃产品;中等品质的渣油加氢裂化柴油和焦化柴油则可通过柴油加氢裂化增产芳烃原料;而高品质直馏柴油可根据市场需求来选择是直接采用加氢精制技术生产柴油产品,还是通过加氢裂化工艺增产芳烃原料、航煤产品和乙烯原料。通过对柴油资源进行群组管理和多途径转化,芳烃产量增加,油品质量更加优质。

图2-7 柴油集约化处理
对于石脑油资源,一方面遵循“宜油则油、宜烯则烯、宜芳则芳”的原则进行加工利用,另一方面可依据“市场需求”进行加工路线选择,实现核心产品的集中。如直馏轻石脑油在油品市场需求旺盛时可选择异构化技术生产汽油组分,在油品市场饱和或过剩时,可直接作为乙烯原料。
对于项目副产的大量轻烃资源,在油品质量约束和市场需求驱动下,低价值不饱和液化气、饱和液化气资源可通过叠合、芳构化和烷基化等技术提升油品质量,实现高价值产品最大化。在旺盛的乙烯市场驱动下,饱和液化气可直接作为乙烯裂解原料,不饱和液化气分离出的饱和资源可作为裂解原料,剩余的不饱和资源可继续采用叠合、烷基化、芳构化等技术处理,富集饱和资源,从而实现乙烯资源的最大化和优质化。
2.2.2.2 以联合装置方式对项目方案实施集约化配置
《石油化工企业设计防火规范》(GB 50160—2008,2018年修订版)对联合装置的定义为:“由两个或两个以上独立装置集中紧凑布置,且装置间直接进料,无供大修设置的中间原料储罐,其开工或停工检修等均同步进行,视为一个装置”[4]。工艺装置联合集约设置的优势在于节省占地、节约投资、节能减排、降低操作费用、减少操作和管理人员。联合布置的特征及内容如表2-1所示。
表2-1 联合装置的特征及内容

将装置进行联合的核心定为“开工或停工检修等均同步进行”,主要原因是装置停工检修时发生火灾的概率较高。停工检修时,一旦发生火灾会对正常生产构成极大威胁。
对于虽然不是上下游关系、但有相互关联关系的装置,若通过生产管理及检维修管理保证同开同停、同时维修也可视为联合装置,其装置平面布置可按联合装置考虑。常见的工艺联合装置有如下几种。
(1)常减压蒸馏-轻烃回收联合
该联合既有物料集成也有热量集成。常减压产生的直馏石脑油进入轻烃回收装置的吸收稳定装置作为吸收油,回收气体中携带的轻烃,再进行解吸。两个装置高度热联合集成,轻烃回收稳定塔底重沸器采用常减压蒸馏的常二中作为热源,石脑油分馏塔底重沸器采用常减压蒸馏的常一中作为热源,脱吸塔中间重沸器则采用重石脑油作热源等。
(2)催化裂化-气体分馏-甲基叔丁基醚(MTBE)-烷基化-汽油脱硫联合
联合装置的物料为上下游直接进料,催化裂化生产的汽油到汽油脱硫装置进行脱硫,汽油脱硫装置生产的含SO2再生尾气再送回到催化烟气脱硫设施进行处理。催化裂化生产的不饱和液化气直接送到气体分馏装置进行分离。气体分馏装置分离出的C4组分依次送至MTBE和烷基化装置作为原料。该联合装置往往也有热量集成到其中,如催化裂化装置主分馏塔循环物料产生低温热作为气体分馏装置塔底重沸器的热源。
(3)催化重整-加氢裂化联合
往往将催化重整产生的氢气经提纯后送至加氢裂化装置作氢源,而将加氢裂化装置生产的重石脑油作为重整装置的原料,两个装置进行联合布置。
(4)不同加氢装置联合
由于不同类型的加氢装置可共用同一氢源,尾气可以到同一变压吸附(PSA)装置进行提纯处理,循环氢脱硫可以共用同一溶剂再生装置来的贫溶剂等,公用部分较多,往往将几套加氢装置进行联合布置。
(5)溶剂再生-酸水汽提-硫磺回收联合
炼厂硫磺回收装置的进料基本为溶剂再生和酸水汽提的酸性气,往往酸性气的压力较低并且远距离输送有安全风险,因此炼厂的溶剂再生、酸水汽提和硫磺回收基本按联合装置布置。该联合集成见图2-8。

图2-8 溶剂再生-酸水汽提-硫磺回收的联合集成
(6)以“渣油加氢-催化裂化”为核心的联合装置
在石化企业中,常以催化裂化或催化裂解装置为核心与上下游工艺装置进行装置群组构建和装置技术集成,目的在于充分利用催化裂化装置副产的催化柴油、催化循环油等劣质资源,以提高装置的汽油收率或高价值轻烃收率。典型的联合装置群组有“渣油加氢-催化裂化”装置群组和“催化裂化-催化柴油加氢”装置群组,相应的集成技术有“渣油加氢-催化裂化”双向组合技术(RICP)、选择性催化裂化工艺技术(IHCC)和LTAG等,这些集成技术已成为石化企业提高资源利用率和提质增效的关键技术。
对于催化重循环油的利用,传统流程一般是将催化重循环油在催化裂化装置内进行循环转化;但由于芳烃含量高,催化重循环油直接裂化容易造成高价值的液体产品收率下降,外甩油浆、干气和焦炭收率增加。RICP则通过构建“渣油加氢-催化裂化”装置群组,从群组资源综合管理利用角度出发,通过改变催化重循环油的循环路径,即先将其经渣油加氢处理后再循环回催化裂化装置(见图2-9),一方面大幅改善了渣油加氢装置的原料性质,另一方面提高了催化裂化的液体收率。与传统流程工艺相比,采用联合装置集约化技术配置后催化裂化装置的汽油收率提高了2%左右。

图2-9 “渣油加氢-催化裂化”联合装置RICP技术
与RICP类似,IHCC也是通过建立技术集约型装置群组实现催化循环油高效利用的集成技术(见图2-10)。IHCC从催化循环油的“分子炼油”理念出发,通过设置单独的循环油定向加氢装置,实现了多环芳烃的定向加氢饱和,加氢后循环油的催化裂化性能明显改善。与常规路线相比,采用联合装置技术后催化裂化装置的汽柴油收率提高了13%左右,资源的利用率提高,全厂经济效益明显改善。

图2-10 “催化裂化-循环油加氢”联合装置的IHCC技术
此外,联合装置的资源管理利用模式也可以实现劣质催化柴油的高附加值转化。如LTAG以“催化裂化”为核心建立了“催化裂化-柴油定向加氢”的联合装置(见图2-11),实现了低品质的催化柴油高效转化为高附加值的催化汽油或芳烃(BTX)。在催化裂化单元,加氢催化柴油的单程转化率大于70%,汽油选择性接近80%,汽油和液化气的选择性高达90%。

图2-11 “催化裂化-柴油定向加氢”装置群组的LTAG技术
(7)重整芳烃装置联合
芳烃生产流程长、装置单元多,换热过程较为复杂,构建联合装置可发挥芳烃原料资源的集中管理利用优势,实现资源的高效转化和能量的综合利用。芳烃联合装置群组通过装置单元的紧凑布置,装置之间可直接采用热进料,避免了物流的重复加热,节省了大量能耗;同时通过装置之间进行物流的热联合和低温热利用,大大降低了装置整体能耗。图2-12为重整芳烃联合装置加工流程简图。

图2-12 重整芳烃联合装置加工流程
(8)环保处理装置联合
对于环保装置而言,可将酸水汽提、溶剂再生和硫磺回收三套装置联合,以便于资源的清洁生产过程管理,减少安全环保风险。通过物流联合型装置群组的建立,酸水汽提装置、溶剂再生装置与硫磺回收装置之间不仅实现了短流程直供料,避免了高浓度的酸性气在厂区内的长距离输送和压力损失,减少管线的腐蚀危险,保证了装置的安全运行和清洁生产;而且通过各装置之间的蒸汽利用优化,联合装置的整体能耗水平也大幅下降。
2.2.2.3 以全厂装置联合方式实施流程规划的集约化
除同类装置的联合集约设置以外,对炼油厂、化工厂、芳烃厂等多个功能厂区进行统一考虑,将装置群作为集约化实施的装置资源,通过全系统、大范围的联合集约,使得总加工流程更为流畅,节省装置占地面积,降低厂区间物料输送储罐的储存时间,减少管理的界面,定员大幅减少,对于企业产品竞争力的提升,以及管理成本的节约具有促进作用。
(1)典型的炼油-乙烯一体化流程集约化配置
在石化工程中,各个不同功能厂区联合形成炼化一体化的生产企业,为石化产品集约化生产模式提供载体,可优化资源配置和产品结构,扩大市场空间,增强积极应对市场变化的能力,提高经济效益。通过炼油、化工一体化的流程安排,优化各个工艺过程的原料,可最大限度地降低化工原料的成本[5]。与单独的炼油厂和单独的化工厂相比,一体的联合企业具有占地面积更少的厂内、厂外以及公用工程设施,土地资源集约使用。典型的炼化一体化模式见图2-13。

图2-13 典型的炼化一体化模式
从图2-13可以看出,原油经过炼化一体化企业的炼油厂加工处理后,生产符合市场质量标准要求的汽油、煤油、柴油等燃料产品,通过公路、铁路和水路等不同运输方式,源源不断输送到不同的客户终端。
生产过程中产生的饱和液化气、拔头油、石脑油、加氢尾油等产品经过管道以及相应的缓冲储运设施后,直接供给化工厂的乙烯生产装置,经过裂解单元裂解,再经冷却、分离处理后,产生的聚合级乙烯、聚合级丙烯等中间原料,再经过管道直接供给下游的聚乙烯、聚丙烯、环氧乙烷/乙二醇等装置进行再次加工处理后,生产出符合市场要求的聚乙烯、聚丙烯、乙二醇等产品,通过不同的运输方式,送往精细化工生产企业作为原料使用。在化工厂乙烯、丙烯等主要中间产品的生产过程中,产生的氢气、燃料气等资源,在满足自身装置需要的同时,富余部分将直接并入炼油厂相应供应系统内,实现了物料直接的互供。同时聚烯烃装置反应所需的1-丁烯等共聚物,也通过炼化一体化流程提供,实现了全厂物料互供,减少外部采购的品种和数量,为企业生产运营成本的降低提供了可能。
(2)化工型炼油-乙烯一体化流程集约化配置
由于装置规模的扩大,石化企业逐渐从分散向集中,从单一向联合,从粗放向集约模式转变。从近年来新建的或者改造的石化工程来看,千万吨级的炼油和百万吨级的乙烯已经逐渐成为标配,新的全厂总加工流程模式的转变,适应了集约化、智能化石化工业发展的趋势,保障了国家能源战略安全,满足了国民经济发展的需要。市场需求的变化,也给炼化一体化全厂总加工流程的调整指明了方向。炼油厂以往的功能是生产汽油、煤油、柴油等油品,集约化流程配置的主要目的是提高原油资源的利用率,多生产油品,随着市场变化,尤其是新一轮能源革命的影响,油品需求的总量在下降,结构在调整,柴油产品面临较大的销售压力,在此种市场形势的影响下,炼化一体化提供了解决方案,炼油厂从油品型向化工品型转变,主要为下游化工厂提供裂解原料,通过蒸汽裂解获得乙烯等单体产品,用于发展高附加值的化工衍生物[6]。化工型炼油-乙烯一体化流程如图2-14所示。

图2-14 化工型炼油-乙烯一体化流程
(3)炼油-乙烯-芳烃一体化流程集约化配置
近年来,为满足芳烃产品的需求,尤其是对二甲苯产品的需求,炼油-乙烯一体化流程逐渐向炼油-化工-芳烃一体化转变。炼油-化工-芳烃一体化模式见图2-15。

图2-15 炼油-化工-芳烃一体化模式
对于原料及产品资源,优质的乙烯裂解原料为富含链烷烃的轻烃,而芳烃原料为富含环烷烃的重石脑油馏分;乙烯裂解产生的裂解汽油富含芳烃,可作为芳烃原料,其抽余油富含环烷烃,为优质的重整原料;而重整汽油的抽余油基本为链烷烃,又是非常优质的乙烯裂解原料。在炼油为乙烯裂解和芳烃分别提供优质原料的同时,重整的副产品氢气和乙烯裂解副产的甲烷氢又可送至炼油装置作为氢源。这种一体化的模式使得炼油生产的副产品能得到最大化的利用,乙烯和芳烃生产过程中富余的氢气、燃料气等资源可以通过一体化装置的集中处理,真正做到“宜油则油、宜烯则烯、宜芳则芳”。
(4)非乙烯路线炼油-芳烃-乙烯一体化流程集约化配置
受乙烯产品市场需求的影响,传统的炼油-芳烃-乙烯一体化流程中,对于乙烯装置以多产乙烯为主。近几年,国内对非乙烯路线炼化一体化进行了深入的研究,通过优化调整炼油厂的加工流程,选择合适的工艺技术路线,利用价值相对较低的重质原料增产以丙烯为主的低碳烯烃产品,以乙烯、丙烯等低碳烯烃产品为载体,发展具有一定规模、有特色、竞争力强、差异化的化工产品。该一体化过程可在炼油厂加工流程中一步实现,不需二次转化。原料为价值相对较低的重质原料,而不是优质的石脑油资源。一体化的载体以丙烯为中心,以发展丙烯衍生物为主要目的[6]。该一体化模式见图2-16。

图2-16 非乙烯路线炼化一体化模式
从图2-16可以看出,该一体化流程的核心是用重油作原料,生产富含丙烯的气体和富含芳烃的石脑油组分,不生产油品,可实现在炼油厂一步生产出烯烃和芳烃。丙烯的生产成本相对较低,用短流程延长产业链,丰富炼油产品结构,提高企业的综合竞争力。
2.2.2.4 以总流程优化平台为基础实施流程规划的集约化
资源的信息化管理是实施项目资源统一配置和优化利用的基础,也是评估资源集约化程度的重要方法。对于总流程规划而言,资源的信息化管理和优化配置主要通过全厂总流程优化平台来实现,见图2-17。可以看出,全厂总流程优化平台的功能主要包括资源信息管理和资源配置优化,其中资源信息管理主要针对项目原料资源、技术资源、产业政策和市场需求等信息进行集中管理和综合分析,资源配置优化主要针对原料利用、装置配置、公用工程和投资效益进行项目整体优化和效益评估。

图2-17 全厂总流程优化平台的资源管理利用
全厂总流程优化平台以项目“资源配置优化”为目标实施总流程集约化评估工作。当评估结果与项目的设定目标存在较大偏差时,则需再次进行资源识别、资源的特征分析和资源的配置优化过程,以最终实现企业的产品结构、经济效益、节能降耗、安全环保等单一目标,并保证企业多个目标的协调统一。可以看出,总流程规划集约化是基于企业“多目标”的实现不断进行的资源管理利用和价值提升过程。
(1)总流程优化平台功能
总流程优化平台以实现企业效益最大化为优化目标,利用线性规划、递归等技术建立数学模型,模拟企业的生产经营过程,功能强大,应用范围广泛。具体功能如表2-2所示。
表2-2 总流程优化平台功能表

(2)总流程规划数字化工具
总工艺流程规划所使用的数字化工具软件主要有炼油厂总工艺流程优化系统、原油评价数据库分析管理系统等,其平台结构如图2-18所示。

图2-18 总流程优化平台结构
(3)总流程优化平台使用方法
总流程优化平台的使用方法如图2-19所示。

图2-19 总流程优化平台使用方法
以炼油规划模型的开发为例,具体建模步骤如下:
①收集原油和产品的市场信息(Supply/Demand模块)。
②确定原油品种、加工量、产品类型及规格,规划不同加工方案。
③通过原油数据库系统软件进行模拟,生成侧线馏分的收率和性质表,并设置常减压装置的物流信息(Distillation模块)。
④设置产品规格和调和组分(Blending模块)。
⑤收集装置的加工信息(物料平衡、物流性质和公用工程),建立二次加工装置模型(Submodels模块)。
⑥在杂项表和递归表中输入需要传递的物流性质(Miscellaneous和Recursion模块)。
⑦模型构建完毕后,进行模型检验。
⑧模型运行。
【案例2-1】 海南炼油项目总流程规划集约化
海南炼油项目采用总流程规划集约化方法,全厂商品收率高达93%,清洁汽煤柴油品收率高达81%,硫磺回收率高于95%,占地0.146公顷/万吨原油,定员仅500人,废气废水排放指标远优于国家允许排放标准,全厂“零废渣”外排,企业在产品质量、经济效益、生产成本、能耗水平、安全环保等各方面指标均达到了国际先进水平[7,8]。
(1)项目采用原料资源群组集约化管理方法,实现了低价值资源的高效利用和高价值资源的回收,提高了资源有效利用率。
①通过加氢装置的低分气集中脱硫和PSA提纯回收,炼厂每年回收纯氢8000t,约占氢气需求总量的10%,节省制氢成本。
②将饱和气体资源与不饱和气体资源分别加工利用,实现高附加值产品(乙烯-聚丙烯-MTBE)的回收。
(2)项目基于“分子炼油”理念,以“产业政策”和“市场需求”为导向,选用了“多产异构烷烃的渣油加氢-催化裂化工艺技术(MIP技术)”组合路线,实现了油品的最大化生产。与单一催化路线相比,项目的油品收率提高了3%~4%,催化汽油和催化柴油的收率高达70%,最大限度利用了原油资源。
(3)项目采用装置群组管理方法,将15套工艺装置分为4个大的装置功能区,并构建了8套联合装置群组。群组内部通过资源(工艺资源、设备资源、外供系统资源等)的联合管理利用,降低了能源消耗,节省土地、设备等投资,同时降低安全环保风险。
(4)项目采用“源头控制、末端治理”的资源环保型加工路线,实现企业的清洁化生产和绿色排放。在源头上采用了全加氢型路线,全厂加氢能力与原油蒸馏能力比值高达97.5%,达到了国际先进水平。通过源头加氢,全厂实现“零废渣”,同时催化原料的硫含量大幅降低,再生烟气中SOx、NOx排放量也相应减少,为烟气清洁化排放奠定了基础。在末端,对酸性水汽提、溶剂再生、硫磺回收进行装置联合,对所有资源进行群组管理和集中利用,通过源头控制和末端治理相结合,保证了全厂安全生产、绿色排放和长周期运行等要求。