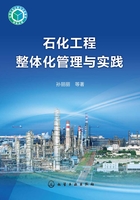
2.4 能量利用集约化
2.4.1 能量利用集约化目标和方法
石化企业在生产能源的同时,也在大量消耗能源。随着节能技术的不断成熟和工程设计的优化,石化企业能耗水平与传统相比明显下降,但油品质量不断升级,需要增加额外的生产装置、处理工艺和能源,必然增加石化企业能耗,在一定程度上减缓能耗数值的降低趋势[11]。
(1)目标[12]
面对全新的节能减排形势和石化企业能源消耗现状,推进石化企业能量全局优化,无疑是解决当前石化企业节能降耗工作瓶颈的有效方法,可以进一步合理降低石化企业能源消耗水平,提高能量利用效率,为开展能量全局优化工作提供方法和技术支持。
热集成是石化生产过程能量系统优化研究的重要组成部分。近年来,研究者对石化生产过程热集成问题进行了较深入的研究,主要涉及工艺装置或子系统集成优化、整厂分析、全局集成等,方法主要包括基于热力学的分析方法和数学规划方法,或二者的综合运用。其中,夹点技术是以热力学原理为基础,以最小能耗为主要目标的换热网络综合方法,是热集成的基础。目前,针对石化生产过程热集成的研究已经取得了丰硕的成果,但如何将丰富的成果整合成为系统、易操作的热集成方法和策略,用于指导石化生产过程工程设计、技术改进再设计等应用过程,值得深入分析。
基于夹点技术,在分析、整合工艺装置物流热输出、热输入原则,凝炼热集成物流温度与热量确定方法的基础上,借鉴集约化管理理论知识,提出适用于工程设计、技术改进再设计过程的石化企业多装置热集成策略,给出相对清晰的多装置热集成实施步骤,并结合应用实例分析,验证策略的实用性,为石化企业过程热集成优化设计、生产提供理论和实证支持。
(2)方法
面对全新的节能减排形势和产业发展现状,要做好石化工程项目能量利用的集约化,需要从全局出发,做好能量优化的顶层设计,以能量深度集成优化为抓手,深入推进全流程综合节能技术的应用,提升石化企业的节能水平[3]。
如图2-23所示,能量深度集成优化以全厂能耗为考核及优化目标,建立总流程规划集约化平台、工艺设计集成化平台、能量集成设计平台之间的相互关系。总加工流程的原料性质、产品分布直接影响全厂能耗水平;工艺装置的流程模拟能具体到装置级别、设备级别的能耗数据;能量集成设计平台包括热集成平台、蒸汽动力优化模型、氢气系统模型、水系统模型、物料输送压力能系统模型等,涵盖了能源的制备、转换、存储、分配及输送环节。

图2-23 能量深度集成优化系统
能量深度集成优化系统的具体措施是[3]:
①以PIMS等线性规划软件为工具,建立节能与总加工流程模型之间的函数关系,实现同步优化和双向提升。
②将原料性质、工艺流程、产品结构、质量要求、装置参数等作为输入条件,建立从全局到装置再从装置到单元的梯级系统能源规划体系,实现不同层级的能量最优化利用。
③结合总平面布置综合考虑水、电、蒸汽、风等公用工程及辅助设施的合理配置,实现系统的最优化配置。
④充分利用石化企业低温、余压资源“集成回收”,通过设置全厂性的利用系统,实现低阶资源的“分布式利用”。
⑤梳理研究季节性温差对燃动系统的影响规律,实施复杂工况燃动系统优化,降低波动。
2.4.2 能量利用集约化的过程实施
开展石化企业节能工作首先需要面对的问题是:石化企业能源消耗与哪些因素相关?一般认为,影响新建石化企业能源消耗水平的因素主要包括:原油性质、总加工工艺流程、产品结构和产品质量,对于已经投产运行的石化企业,还要关注装置负荷率等影响因素。其中,工艺总加工流程不仅可以影响石化企业能源消耗,而且对石化企业的产品结构、产品质量也具有重要影响。石化企业总加工工艺流程是综合权衡资源、能源、环境、效益等因素后,多目标协同优化确定的。因此,以降低石化企业能源消耗为目标的总加工工艺流程优化(装置规模与装置结构优化)是开展石化企业能量利用集约化的重要步骤。
石化企业原油性质、总加工工艺流程确定后,产品结构、产品质量、装置负荷率等可以确定,石化企业的能源消耗结构和能源消耗水平也随之确定。此时,石化企业能源消耗存在工程极限值,工程极限值主要受当前经济技术条件约束。针对特定的石化企业能源消耗结构,可以合理规划企业的能源配置系统;而明确的能源消耗工程极限值有助于合理制定节能目标,进而应用各种节能技术提高石化企业能量利用效率,进一步降低其能源消耗水平,使石化企业能源消耗趋近于工程极限值[11]。
本书所阐述的石化工程项目能量利用集约化方法将石化企业能量利用工作划分为能源规划、能量集成、单元强化三个层次,如图2-24所示。

图2-24 石化企业创新系统化节能方法
2.4.2.1 对于全局能量实施能源规划层次的集约化利用
无论是新建、改扩建,还是已经投产运行的石化企业,开展节能工作的首要步骤是优化调整石化企业总加工工艺流程。能源规划的具体步骤有以下几点。
①以石化企业原油性质与产品信息为基础,以资源、能源、环境、效益等要素协同优化为目标,通过综合权衡和多目标优化,确定石化企业总加工工艺流程。
②以总加工工艺流程为基础,分析石化企业能源消耗结构,测算石化企业能源消耗工程极限值与燃料、电、蒸汽、水、氢气的需求数据。
③对比分析能源消耗工程极限值与运行(设计)能源消耗值,制定节能目标,提供能源配置规划建议。能源规划建议主要涉及:燃料需求、热工锅炉设置、电力需求、蒸汽平衡、循环水场设置、制氢规模设置、氢气管网设置、热集成等方面。
④结合节能目标和能源规划建议,将能源消耗指标分解至各石化生产装置、公用工程与辅助系统,作为指导和约束能量集成与单元强化层次开展工作的指标。
2.4.2.2 对于装置实施能量集成层次的集约化利用
能量集成主要完成石化生产装置、公用工程、辅助系统的用能优化,是落实石化企业能源规划的关键组成部分。图2-25为石化企业能量全局优化策略示意图,该策略提供了实施石化企业能量全局优化的逻辑关联关系。

图2-25 石化企业能量全局优化策略
①进行工艺装置的用能优化,包括反应、分离等核心过程工艺改进和参数优化。
②在此基础上,一方面开展氢气系统的优化,另一方面建立装置间热联合和优化换热网络等。
③随后开展罐区和辅助系统的用能优化,按照温位匹配、梯级利用的原则,通过优质热阱的挖掘与应用降低不必要的蒸汽或其他高品位能量的消耗,然后对全厂的低温热综合回收利用,按照“长期、稳定、就近”利用的原则,结合全厂平面布置,设计合理的低温热系统,同时开展循环水系统的用能优化。
④优化蒸汽动力、燃料系统,包括蒸汽管网和凝结水系统等,结合全厂蒸汽需求、动力需求和燃料平衡状况,对蒸汽动力与燃料系统提出优化的改造和运行策略。
2.4.2.3 对于元件实施单元强化层次的集约化利用
单元强化是实现石化企业能量全局优化的重要基础条件,主要涉及关键耗能设备的强化、优化利用。通常石化企业关键耗能设备包括:工艺装置反应设备;工艺装置余热与余压回收系统设备设施;功率不低于10MW的加热炉;轴功率不低于1000 kW的容积式压缩机;轴功率不低于2000 kW的离心式压缩机;轴功率不低于200 kW的机泵等。单元强化的主要实现方式是对单个过程、单元或设备开展节能专项技术改造或应用。
【案例2-3】 炼油厂能量集约化规划和应用
(1)能源规划
某炼油企业设计主要产品包括:液化气、航煤、汽油、柴油、硫磺和聚丙烯等,产品质量执行国Ⅴ标准,总加工工艺流程见图2-26,设计能耗数据见表2-5。

图2-26 某炼油企业总加工工艺流程(单位:万吨/年)
表2-5 某炼油企业设计能耗数据

基于上述基础数据,应用REMS系统进行测算,测算结果汇总于表2-6。
表2-6 某炼油企业能源消耗数据测算结果

工程极限值为节能目标的确立奠定了基础,设计燃料气、电消耗量与测算工程极限燃料气、电消耗量存在一定差值是导致设计能耗与工程极限能耗数值不同的主要原因。结合表2-5与表2-6的数据分析,提供能源与耗能工质的规划建议:
①燃料气与热集成。适当强化热集成,合理提升进入加热炉、分馏塔工艺物流的换热终温,适当降低燃料气、分馏塔热源蒸汽消耗量。
②蒸汽优化。企业3.5MPa蒸汽与1.0MPa蒸汽过剩,0.4MPa蒸汽不足。根据蒸汽系统类型,建议3.5MPa、1.0MPa、0.4MPa蒸汽满足工艺需求后,工艺过程发生的3.5MPa、1.0MPa蒸汽的热量可适当调整为直接热集成。
③电力使用。合理利用工艺余压发电,适当以蒸汽为动力源驱动动设备,降低电消耗量。
(2)能量集成
根据企业能源消耗特点,采取如下能量集成措施。
①优选节能工艺、催化剂,合理降低反应苛刻度,从源头降低工艺总用能。
②结合装置布局,重点考虑原油蒸馏-渣油加氢-催化裂化装置间的热量集成,考虑加氢精制装置间的热量集成。
③按照“温度对口、梯级利用”原则,优化蒸汽动力系统,避免蒸汽降质使用。
④结合装置布局,设置局部、全厂性的低温热回收管网,全局回收、利用低温热资源。
⑤优化循环水系统,适当考虑循环水的梯级利用。
⑥理顺装置间工艺物流压力等级,避免装置间压力的重复升、降,合理节约耗电量。
能量集成层次中,原油蒸馏-渣油加氢-催化裂化装置间的热集成与全厂低温余热资源利用是两项关键节能措施。其中,原油蒸馏-渣油加氢-催化裂化等主要耗能装置之间的热联合主要包括装置内热量集成、热供/出料及其温度优化,以及不同装置物料间的直接换热等。集约化改造思路如图2-27所示。

图2-27 主要耗能装置热联合集约化改造思路
热集成实施后,初底油换热终温可达290℃,将290℃的原油与335℃左右的油浆换热,原油温度升至约310℃后返回进常压炉,预计节约燃料气1.5t/h,减产3.5MPa蒸汽约24t/h。
对于低温热资源,在设计工况的基础上,全厂设置低温余热回收系统,回收80~120℃热媒水,设置的两个系统为:
①罐区维温与管线伴热低温热利用系统:回收低温余热供罐区维温与管线伴热,预计每小时回收低温热1.2MW。
②低温热发电系统:回收热媒水约1000t/h,集中发电,热电效率以6.0%计,预计每小时发电2.5MW。
(3)单元强化
单元强化措施如下:
①采用强化燃烧及烟气余热回收技术,合理提升工艺加热炉热效率。
②合理提升列入关键耗能设备的压缩机效率。
③合理提升列入关键耗能设备的机泵效率等。
该炼油企业大型工艺加热炉设计热效率为91.0%,重整四合一炉热效率为92.0%,结合燃烧强化技术与烟气余热回收技术应用,优化提升大型工艺加热炉热效率至93.0%,提升重整四合一炉热效率为94.0%,预计节约燃料气约1.0t/h。主要涉及的加热炉如表2-7所示。
表2-7 某炼油企业大型工艺加热炉

(4)节能效果
采用集约化的能量系统优化方法后,节能优化工作取得了突出成效:按照能源规划、能量集成、单元强化建议,并结合关键节能措施实施,优化后设计能耗数据见表2-8。优化后,该企业设计炼油能耗及设计炼油单位因数能耗相对于优化前的设计数据降低约5.0%。
表2-8 某炼油企业优化后设计能耗数据
