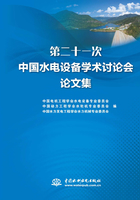
上QQ阅读APP看本书,新人免费读10天
设备和账号都新为新人
1 主泵模型与参数
1.1 主泵模型
为了全面分析泵的水力性能,以及分析不同流道之间的相互影响,因此在此次优化过程中,以主泵整体流道的优化为主。如图1所示,在整体流道CFD计算中,包括进口域(吸水室)、叶轮域(混流式叶轮)、导叶域(导叶)和环形蜗壳域(环形蜗壳)。主泵无量纲比转速ns按式(1)计算[9]:

式中:Qd为设计流量;Hd为设计扬程。
根据给定的流量和扬程计算出该泵比转速处于混流泵范围,因此叶轮设计按混流泵设计。

图1 主泵模型流道示意图
1.2 叶轮与导叶原始设计方案
图2为叶轮初始设计方案示意图。初始方案叶轮具有4个叶片,根据提供的水力参数初步计算,以及叶轮扬程的需求,参考现有比转数为650左右的混流泵,进行该混流泵叶轮的初步设计。在叶轮初步设计时,仅对叶轮流道进行CFD计算,通过多轮叶轮单独优化设计,初步得到混流泵的叶轮,作为后续全流道优化设计的初始叶轮。该混流泵导叶设计的好坏直接影响导叶自身的水力损失和环形蜗壳内的水力损失,对于泵整体的水力性能好坏起到了关键作用。因此,在导叶设计时,进行了全流道的CFD计算及分析,由于该混流泵的导叶设计并没有可参考的水力模型,因此在该导叶设计时,进行了大量的优化设计比较。初始方案导叶具有9个叶片,如图3所示。

图2 叶轮初始设计方案示意图

图3 导叶初始设计方案示意图
1.3 数值模拟与优化方法
研究采用CFD数值模拟对主泵的内部流动进行预测。CFD模拟中,求解三维不可压缩黏性湍流,湍流模拟方法为雷诺时均法(RANS),湍流模型为SST k-ω模型[10]。计算域和网格如图4所示,其中吸水室与蜗壳使用非结构网格,叶轮与导叶使用结构网格。经过网格无关性检查,最终采用的网格节点数见表1。

图4 CFD计算域与网格示意图
表1 计算域网格类型及数量
