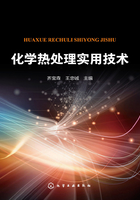
2.4 渗碳质量控制
2.4.1 渗碳(碳氮共渗)设备
①渗碳(碳氮共渗)加热设备有效加热区内的温度允许偏差不得超过表2.135中的规定范围。
表2.135 渗碳和碳氮共渗加热设备有效加热区的温度允许偏差

②气体渗碳(碳氮共渗)炉有效加热区检验合格后,还需进行渗层深度均匀性的检验。试样安放位置可参照加热炉有效加热区保温精度检测热电偶布点位置(表2.136和表2.137)。同炉处理各试样的有效硬化层深度偏差应符合表2.138的规定。
表2.136 周期井式热处理炉检测点数量和位置

表2.137 周期箱式热处理炉检测点数量和位置

表2.138 渗碳和碳氮共渗炉有效加热区内有效硬化层深度偏差值要求 单位:mm

③以燃气、燃油、燃煤为热源的固体渗碳炉,其火焰不能直接接触渗碳箱。
④连续式加热炉应满足渗碳和碳氮共渗各阶段的工艺要求。
2.4.2 渗碳过程的质量控制
(1)渗碳方法的选择 渗碳方法很多,常用渗碳方法的特点见表2.139。目前生产厂家广泛使用的是气体渗碳,固体渗碳适用于少量生产,真空渗碳是渗碳工艺的发展方向。
表2.139 常用渗碳方法的特点

(2)工艺参数的选择 见表2.140。渗碳工件的质量,首先,渗层的表面碳含量、渗层深度和碳的质量分数梯度三方面需要达到技术要求,渗层深度主要取决于渗碳温度和时间,表面碳含量和碳的质量分数梯度与炉气的碳势高低及其控制精度有关;其次,渗碳后还需进行渗后热处理,达到使用性能。
表2.140 渗碳工艺参数的选择

(3)渗碳设备与渗碳剂的选择 渗碳加热设备应结构合理,设有使炉内气氛均匀流动的装置,渗碳加热室应具良好的密封性,渗碳的原料供给系统应安全可靠。渗碳温度偏差允许在±15℃以内,应选择Ⅳ类以上炉子,其控温精度、仪表精度和记录纸刻度等要符合Ⅳ类以上炉子的技术要求,并具炉气碳势控制功能。加热炉分类及技术要求见表2.141。
表2.141 加热炉分类及技术要求

①允许用修改量程的方法提高分辨力。
渗碳剂在渗碳过程中产生活性碳原子,并渗入工件表面,故要求渗碳剂纯度要高、成分波动小,对渗碳剂要有明确技术要求的专门标准,对工件不会产生有害影响。主要渗碳剂技术标准见表2.142。气体渗碳剂主要有天然气和液化石油气等,要求其丙烷或丁烷纯度在90%(质量分数)以上,所以应采用高纯度渗剂气源。
表2.142 主要渗碳剂技术标准

注:渗碳剂应有生产厂家质量保证单或合格证。不合格产品禁止使用。
①热处理设备质量控制。热处理设备应能满足零件渗碳热处理所需工作温度和保温精度、碳势控制精度、有效加热区的规格尺寸和测温控温系统;热处理炉有效加热区应定期检测,检测周期见表2.143,其保温精度应符合表2.141相应炉型的保温精度要求。应在设备明显位置悬挂带有有效加热区示意图的检验合格证,加热炉只能在有效加热区检验合格规定的有效期内使用。热处理炉有效加热区按GB/T 9452的规定测试。
表2.143 加热炉有效加热区检测周期及仪表检定周期

热处理炉温度测量系统在正常使用状态下应定期做系统校验。校验时,检测热电偶与记录仪表热电偶的热端距离应靠近,校验应在加热炉处于热稳定状态下进行。系统校验允许温度偏差应符合表2.144规定。
表2.144 系统校验允许温度偏差

当超过允许温度偏差时,应查明原因排除或进行修正后方可使用,非专业仪表人员不得随意调整,校验结果应制成如表2.145所示的炉温仪表校验卡,悬挂在设备上,供操作者参考。
表2.145 炉温仪表校验卡

②工艺材料控制。热处理工艺材料应按技术要求建立定期检验制度,确保热处理质量稳定,检验结果应记录在档案中。
③操作与记录。操作者应严格执行“热处理工艺卡”和“热处理作业指导书”的规定要求,并认真做好记录。热处理记录必须保持完整、清晰、真实。
2.4.3 渗碳操作的质量控制
热处理设备操作人员应经专门培训并持有操作证,熟悉设备的结构、性能、精度和效率等特点,严格按设备操作规程进行操作,达到准确控制工艺参数的目的。渗碳操作过程中应注意表2.146中的内容。
表2.146 渗碳操作过程中应注意的五个方面

2.4.4 渗碳检验的质量控制
2.4.4.1 渗碳检验质量控制的作用
渗碳检验质量控制的作用在于保证产品符合技术要求,不合格产品不能转入下道工序,记录、分析和评价所得检验数据,为质量控制提供依据。
2.4.4.2 检验设备的质量控制
检验设备必须符合相应的标准规定,并定期经技术监督部门检定,保证其检测精度和测量数据的可靠性,检定结果应记录在档案中。
2.4.4.3 检验规程
渗碳质量检验(包括硬度、金相、硬化层深度等)均必须编制相应的书面检验规程或检验工艺卡,检验文件应符合相应的标准和技术要求。
2.4.4.4 随炉试样检验
随炉试样检验的项目名称、具体内容见表2.147。
表2.147 随炉试样检验的项目名称、具体内容

表2.148 不同有效硬化层深度的硬度范围及计量类型

表2.149 渗碳齿轮有效硬化层深度推荐值 单位:mm


2.4.4.5 齿轮渗碳及热处理质量检验
齿轮渗碳及热处理质量检验的项目名称和具体内容见表2.150。
表2.150 齿轮渗碳及热处理质量检验的项目名称、具体内容

表2.151 渗碳有效硬化层深度允许偏差

2.4.5 渗碳件常见缺陷及其控制
渗碳件在渗碳及热处理过程中如果控制不当,往往会出现各类缺陷,缺陷的形成原因及其控制措施见表2.152。
表2.152 渗碳件热处理常见缺陷分析及控制措施




图2.77 常用渗碳钢合金元素的氧化趋势
炉子中平均成分(质量分数):40% H2,20% CO,1.5% CH4,0.5% CO2,0.28% H2O, 37.72% N2。
2.4.6 [实例2.6]球磨机渗碳淬火齿轮轴断裂的失效分析及对策
球磨机破碎比大,可对各种矿石和其他可磨性物料进行干式或湿式粉磨,适应性强,易于实现自动化控制。因此,在选矿、建材、化工、冶金、材料等行业中,球磨机都是最普遍、最通用的粉磨设备。随着企业生产规模的不断扩大和矿石品位的下降,使得球磨机的生产能力越来越大,并使球磨机越来越大型化。
(1)工件名称与使用材料 工件为齿轮轴(其外形结构见图2.78),它是球磨机传动装置上的关键部件,随着球磨机向大型化发展,齿轮轴的使用材料及加工工艺也有所改变,采用的是渗碳钢(渗碳淬火)代替调质钢(调质+局部表面淬火)。

图2.78 齿轮轴外形实物照片
所使用材料为20CrNi2Mo钢,规格为ϕ579mm×3000mm、齿轮模数25、齿数21、左旋7.5°。
(2)热处理技术条件 齿部渗碳层深度2.5~3.0mm,齿面硬度57~61HRC。
(3)加工工艺流程 坯料→锻造→粗车→无损检测→调质(650℃回火)→精车→磨前铣齿→齿部渗碳淬火+回火→磨齿。
(4)现场观察与分析 在用户现场使用过程中,齿轮轴断裂时未发现明显异常,只是在运行中电动机仍在工作,但齿轮轴已不随着旋转。该齿轮轴使用寿命大概在12个月左右。齿轮轴的结构见图2.78,齿轮轴断裂宏观形貌见图2.79。

图2.79 齿轮轴断裂宏观形貌
造成齿轮轴断裂的原因很多,设计、工艺、加工精度、锻造、热处理、安装精度、维护保养等各个环节均可能造成该齿轮轴断裂。由于该断裂齿轮轴为备件,在更换该断轴前的另一根齿轮轴因到使用寿命而失效,说明设计、工艺、加工、安装、维护保养等环节不存在问题。为查找该齿轮轴断裂的主要原因,对其进行了化学成分分析、金相组织观察、断口观察和力学性能测试等。
(5)理化检验与分析 齿轮轴在齿部断裂,在断口分离前,裂痕呈直线状沿周向分布,见图2.79(a)。裂痕及附近区域无宏观塑性变形显示脆性断裂特征。断裂齿轴为径向通透型断裂,见图2.79(b)。
对球磨机断裂齿轮轴进行检测,对断轴进行切割取样,取样情况见图2.80、图2.81。

图2.80 取样情况

图2.81 取样情况对比
①断口宏观检测。对应面断口宏观形貌见图2.82~图2.84。断口平齐,断面可见明显放射状花样。放射状花样的收敛区在偏离圆心的圆形相对平坦区域及略带凹凸位置,该区域距齿顶约250mm,为断裂源区,如图2.82中箭头所示。对应面一侧断口因钻取化学成分分析样品,断裂源区已被破坏(见图2.83箭头),另一侧除断口表面油污较严重外,断面基本无损伤。在断裂源区取样并清洗后(见图2.84),肉眼可见断裂源区沿枝晶开裂特征(枝晶间存在明显台阶)及15mm×10mm和10mm×2mm夹杂物缺陷。

图2.82 齿轮轴断口

图2.83 对应面一侧齿轮轴断口

图2.84 齿轮轴局部断口(断裂源区)
②断口微观检测。用扫描电镜观察了断裂源区及附近断口微观形貌(见图2.85、图2.86),断口显示解理及准解理断裂特征。对断裂源区缺陷(见图2.86)进行了能谱定性及半定量检测,结果表明缺陷部位含有O、Ca、Si、C、Al、Fe、Mg、Na、K等元素,为夹渣缺陷。

图2.85 断口二次电子像

图2.86 断口缺陷二次电子像
③低倍金相组织检测。在断口附近截取了齿轴径向(距断口轴向距离约20mm)及轴向样品,进行了低倍金相组织检测,结果见图2.87~图2.89,图2.88、图2.89试样上表面为断口。依据GB/T 1979—2001标准,低倍组织评定为一般疏松0.5级,无其他低倍组织缺陷,存在较严重枝晶组织,断裂源区枝晶组织尤为严重,渗碳淬火层及调质处理层清晰可见,调质层距齿顶深度约为110mm。

图2.87 低倍组织

图2.88 低倍组织(轴向)

图2.89 断裂源区低倍组织
④金相检测。图2.90为齿轮轴非金属夹杂物检测结果,参照GB/T 10561—2005标准评定为:A类粗系l级,B类粗系l级,C类0级,D类细系2级。图2.91为齿根部渗碳淬硬层组织,组织为M回火,M级别为5级。图2.92为调质层,调质组织为S回火+F,存在枝晶组织。图2.93为调质层附近组织,组织为P+F,存在较严重枝晶组织。图2.94为断裂源区组织,组织为F+P,存在严重枝晶组织,晶粒度≥8级。

图2.90 非金属夹杂物,100×

图2.91 齿根部渗碳淬硬层组织

图2.92 距齿根表层30mm组织(调质层)

图2.93 距齿根表层150mm组织(调质层附近组织)

图2.94 断裂源区组织
⑤化学成分检测。化学成分分析结果见表2.153,参照GB/T 3203—2016标准《渗碳轴承钢》,对化学成分的检测值和标准值进行了对比,齿轮轴检测结果基本符合标准规定。
表2.153 化学成分检测结果(质量分数) 单位:%

⑥力学性能检测。在轴心断裂源区附近沿径向截取了力学性能试样,检测结果见表2.154,参照标准中引用的GB/T 3203—2016材料牌号(G20CrNi2Mo),强度测量值偏低,这与取样位置有关(标准值为纵向取样,且是经淬火+200℃回火后的值)。渗碳淬硬层硬度梯度检测结果见表2.155,渗碳淬硬层深度约3.0mm。距齿根表面调质层硬度梯度检测结果见表2.156。
表2.154 力学性能检测结果与参考值对照表

表2.155 渗碳淬硬层硬度梯度检测结果

表2.156 距齿根表面调质层硬度梯度检测结果

(6)检测结果分析与结论
①参照GB/T 3203—2016《渗碳轴承钢》标准评定,齿轮轴化学成分基本符合标准相关规定。
②在齿轮轴心部断裂源区附近截取了径向试样(拉伸及冲击),检测结果显示,冲击值满足技术条件规定,说明材料具有较好的韧性。强度偏低有两方面原因:ⅰ.标准试样为直径25mm的检测值,而该齿轮轴直径为579mm;ⅱ.应与横向取样及取样时更靠近轴心有关(JB/T 5000.8—2007标准规定的取样位置为距表面1/3半径处)。齿轮轴的齿部渗碳淬火层深度及硬度略低于标准要求。
③由齿轮轴表面至心部金相组织检测结果显示,基体组织无异常,齿轮轴枝晶组织较严重,特别是断裂源附近更为严重,说明在锻造过程中枝晶组织未得到有效的改善,在允许的情况下可适当增大锻造比。枝晶组织严重时会不同程度地降低材料的力学性能。
④齿轮轴显示瞬时(一次性)脆性断裂特征,断裂源区在齿轮轴心部偏离轴心区域。该处存在肉眼可见夹杂物缺陷,且枝晶组织严重,说明该部位是齿轮轴的薄弱区域,易引发应力集中导致的开裂。
⑤齿轮轴在设备运行过程中断裂,且使用时间约12个月。根据齿轮轴为突发一次性断裂的特点分析,其断裂时应存在两种情况:ⅰ.断裂源区承受较大应力作用,该应力可排除齿轮轴制造过程中所能残留的组织应力、热应力等应力作用,也可排除使用过程所形成的热应力及齿轮轴旋转所形成的扭转应力作用。由于齿轮轴运行现场无法提供有效的监控记录及相关数据,因此无法更精准地判断轴心应力的来源。ⅱ.断裂源区相对薄弱。
通过上述分析得出以下结论:齿轮轴心部存在夹杂物及枝晶缺陷,在设备运行过程中,当轴心承受较大应力作用时,在薄弱部位引发了瞬时脆性断裂。
(7)改进措施 引起齿轮轴断裂的原因很多,仅从热加工方面着手,通过提高锻件质量、增加锻后正火热处理工序、增加渗碳前预备热处理(粗铣齿后调质热处理)工序,以及调整最终热处理渗碳淬火工艺参数等手段,提高热加工工艺效果,从而保证产品质量。